Electromechanical Systems Design (24-673)
Carnegie Mellon University, Fall 2021
This project was one of the most time-consuming, rewarding projects I’ve undertaken. We were tasked with building a novel consumer product which involved electromechanical systems. Over the course of the semester, we navigated through the product development process, from conceptualization, market research and customer outreach, concept generation, mechanical design, electronics integration, fabrication, and testing. For this project, I led the project management and electronics integration, as well as contributed heavily to the mechanical design and fabrication.
For this project, we chose to build an automated burger flipper, as a proof of concept for a fully automated frying assistant. See our poster below:
Product Conceptualization
We first started with identifying a product opportunity gap to address. After some discussion, we decided to pursue kitchen automation. Many people wish they could eat more home cooked meals, but lack the time or skill to do so. We intended to address this problem by utilizing automation to minimize the need for individuals to monitor their frying, in a cost-effective and easy-to-use manner.
Several competitors in this space exist, but options are limited and generally expensive. After extensive analysis we determined there was especially an opportunity in consumer kitchen automation, as existing automation products, such as Flippy the Robot, focused more on an industrial scale. We decided to build a countertop kitchen appliance, designed primarily for amateur chefs but also could see some secondary use in food service. To fit within the scope of the class, we chose a simplified approach which focused on only cooking up to 4 patties at once. Below are some of the simplifications we made for this prototype versus what we imagine a final product to include.
Establishing Customer Needs and Addressing Target Specifications
Following identification of individuals cooking in their own homes as our target audience, we created a survey to gather information from potential customers. The survey focused on gathering essential consumer behavior data about cooking habits and needs, general kitchen use, and consumer preferences. We also collected demographic data to identify trends as well. After this survey, we identified 14 customer needs, as well as 4 design team needs. From here we mapped these customer needs, which are qualitative, onto quantifiable metrics. From here, we set targets for our product. Below is a chart with our ideal and marginal target specifications, in comparison to several competitors.
Concept Generation
Following this research and analysis on design priorities and objectives, we moved on to concept generation. We first completed a functional decomposition to identify key functionality as well as how systems would need to interact with each other. This helped us organize our thoughts and break the product down into individual components.
The basis of the product was the ability to take a user input, place the food, monitor and flip food as necessary, and finally remove the food and notify the user. Monitoring is conducted via temperature probing, and a simple user interface allows the user to input commands.
Following this functional decomposition, we then started our internal and external search. Looking externally, we identified key features and technology in competitor products. Internally, we created a number of different concepts focusing on different methods for each function. The goal in this stage was purely identifying possible mechanisms, without regard to the feasibility or cost. As a team, we generated over 40 different concepts. From here, we started to categorize these ideas into different styles of mechanisms. We also combined ideas in new ways to create additional concepts. From here, we selected our top ideas and put them into 2 decision matrices, a Pugh Screening matrix and a weighted decision matrix. These matrices helped show how each of our concepts could fulfill the required metrics and meet our design goals. The final decision matrix can be seen below:
Design, Prototype, and Analysis
From this point, we emerged with a concept product of a 2 DOF spatula system and a 2DOF probe system to both manipulate patties and measure patty temperatures. To go from concept to reality, we first focused on a simplified prototype 1, which focused on the flipping action. We identified this as a critical aspect of our product’s success, and thus dedicated early resources to testing its viability. A CAD model of the system, as well as a short video is shown below.
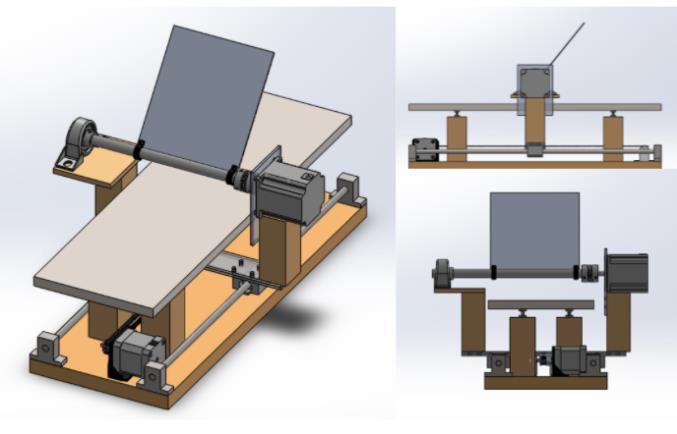
Following this success, we moved into in depth design and analysis. Focus included motor torque analysis, power consumption calculations, finite element analysis, FMEA analyis, dynamics calculations, and finite state models. I also completed a detailed electronics schematic which includes all electronic elements.
Following our detailed design, we moved onto final fabrication. As our product needed to be heat resistant, we placed an emphasis on using primarily metal parts. This means we used mainly conventional manufacturing techniques such as milling, turning, waterjetting, and welding.
Finished Product
More details to come as I continue to work on this page! For now check out the renders and poster above!